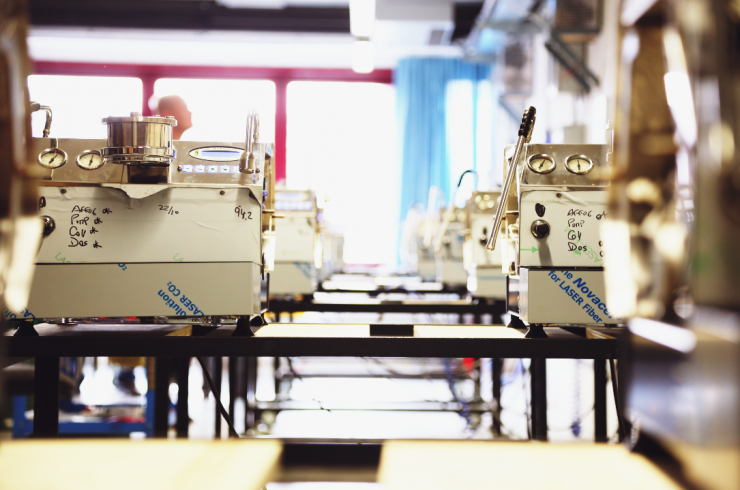
A line of La Marzocco GS/3s.
In 2013, Sprudge was given the opportunity to tour the factory of our friends & partners at La Marzocco in Florence, Italy. Alex Bernson and Kate Beard reported on the factory’s history, its modern upgrades, and the size and scope of the factory itself.
In late 2015, Sprudge returned to Italy to attend Out of the Box in Milan, and a tour group of coffee enthusiasts were invited back to the factory in Florence. This time around I wanted to focus on the people behind the production, and to explore a very specific element of La Marzocco lore.
On most machines, somewhere, there’s the quote “Handmade In Florence”. I personally remember looking at it underneath the digital display of the GB5 espresso machine as a barista, and would imagine an old Italian hammering metal together in a dark, dusty Tuscan farmhouse. This is absolutely not what the real La Marzocco manufacturing looks or feels like, but it’s not entirely far off.
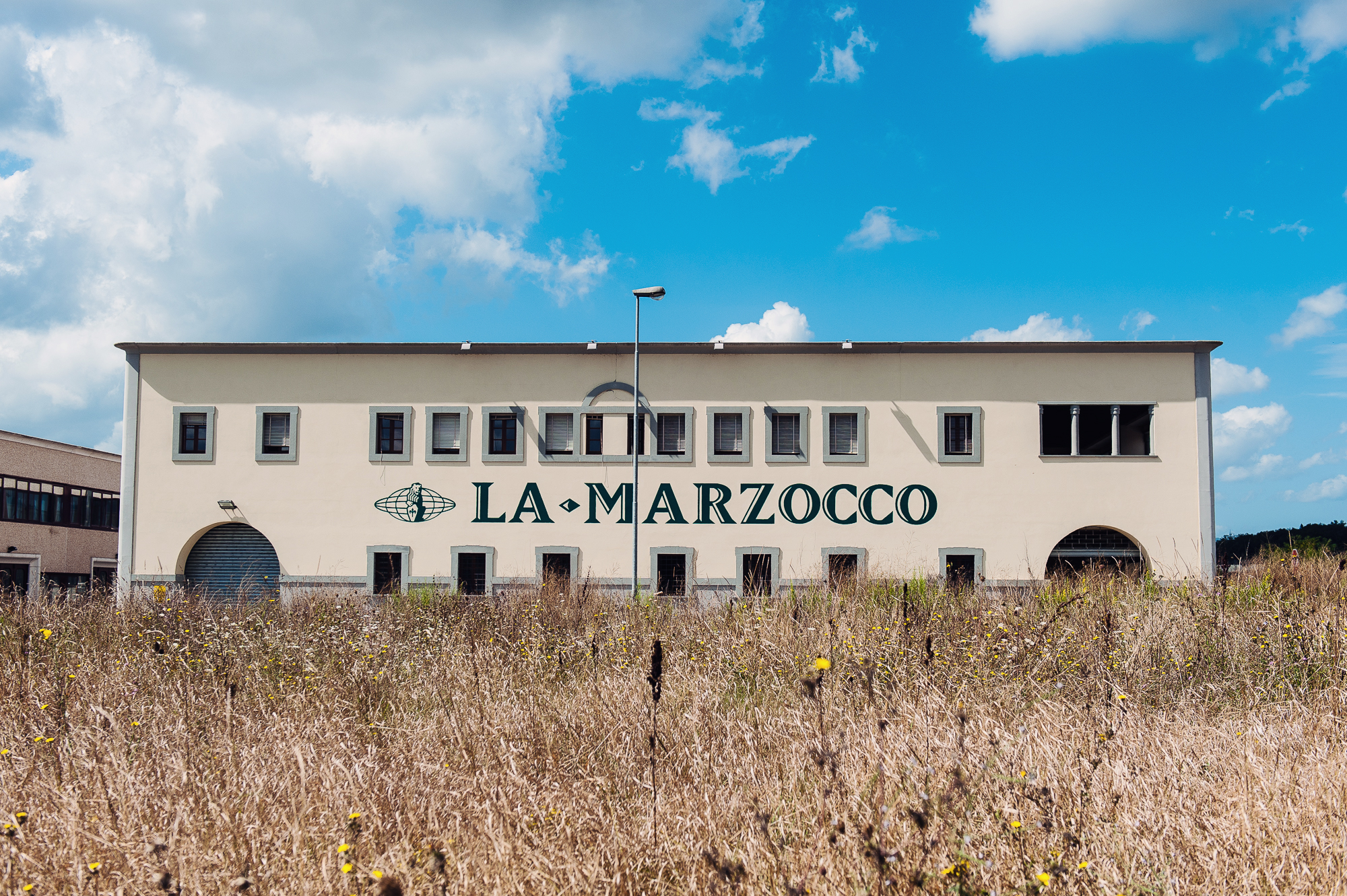
The La Marzocco Factory (File photo by Kate Beard for Sprudge)
The factory is modern, large, and there are multiple hands that are responsible to building an espresso machine. There are many steps in the process of making an espresso machine, and we visited all of the departments that put them together.
During our tour group’s lunch break, I snuck away with La Marzocco’s Lorenzo Santoni, one of the members of the hush-hush Research and Development team. Santoni introduced me to the workers of La Marzocco, and helped translate my interviews with them.
Here are six folks that I had the opportunity to meet, and who are integral in building these machines by hand.
Lorenzo Carcasci
Boilers are the heart of the espresso machine, and Lorenzo Carcasci leads a team of welders responsible for piecing them together. Carcasci has been with La Marzocco for twenty years, one of the longest tenured employees we met at the factory. Carcasci hand welds the boilers at a rate of thirty per day. “It could be faster, but we prefer to take time to ensure quality,” he told us.
Carcasci works on new projects with the Research and Development department. Carasci spent the last several years helping construct the La Curva prototype. La Curva is just one of the prototypes Carcasci has helped build. “If I have an idea, they listen,” Carcasci says, “It’s very good to work in this way.”
Cristian Bartolacci
Once the boilers are built, Cristian Bartolacci and his team assemble them. Bartolacci has been building boilers at La Marzocco for three years. His team builds up to fifty boilers per day. When asked what he liked most about working in the factory, Bartolacci told us, “La Marzocco is a strong group of friends.”
Alessio Gianni
Gianni has been with La Marzocco for six short months, one of the newest employees we met at the factory. His team assembles all the tubes within the boiler and applies a thermal wrapping. Thermal wrapping is a relatively new customization that’s become standard with all La Marzocco espresso machines, a mod that is said to save electricity consumption up to twenty percent.
“We’re not just employees,” says Gianni, “we’re all friends.”
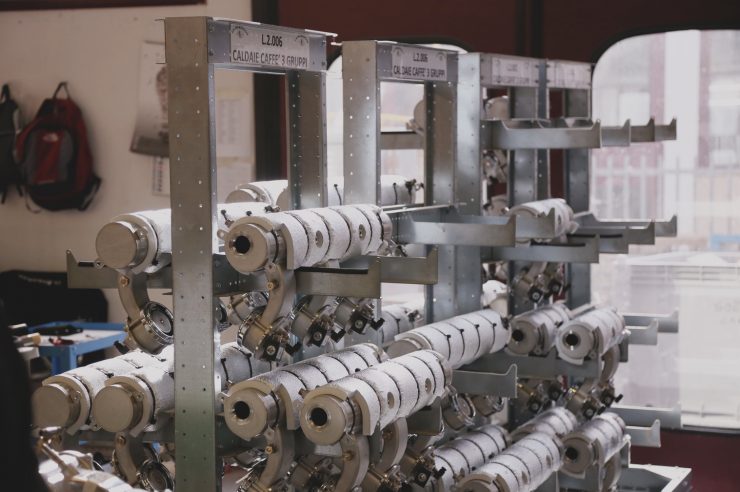
Several boilers wrapped in thermal lining.
Roberto Bigalli
Bigalli works in the electrical department, one of the most intimidating areas of the factory. We counted twelve naked machines being wired together. Surrounding the machines were bays of wire, buckets of tools, and walls of instruments. Each member of the department was responsible for connecting the electrical components.
The process takes time, and Bigalli can complete four to five machines per day. “The time goes by fast here,” he assures me, “Everyone has a good time.”
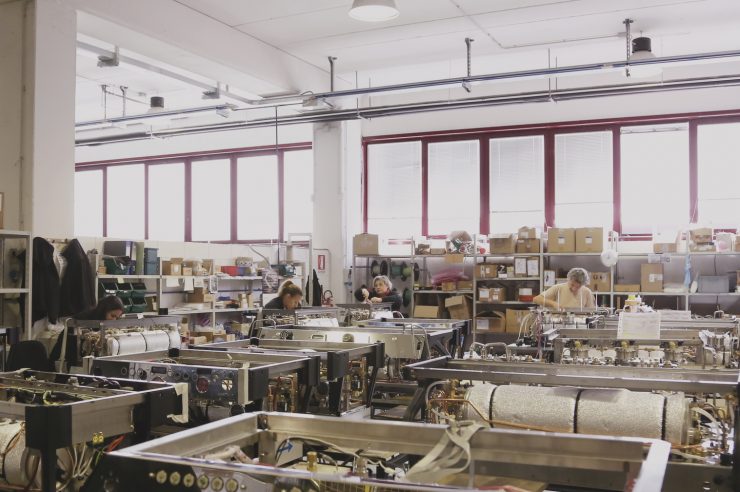
The electrical department.
Felippo Fabiani
For twenty-two years, Fabiani has been building La Marzocco espresso machines. Fabiani is one of the first employees at the factory, and has personally helped build over six thousand machines.
He’s currently bench testing La Marzocco’s new line of Linea PB espresso machines. “Every day feels like the first day here,” he tells me.
Tommaso Bartali
Bartali has worked at La Marzocco for nearly four years and is currently stationed in one of the final steps of espresso machine manufacturing: packing the machine for delivery. Once a machine has been bench tested, it is carefully prepped and placed in a pallet for shipment.
Bartali packs about twenty-five machines per day. Echoing the sentiments of his colleagues, he told me, “We’re all friends here. It’s a pleasure to work in an environment like this.”
The camaraderie is evident throughout the factory in all departments, and a common theme kept coming up with almost every engineer I interviewed: the people here are friends, and just plain like each other.
It’s far from the image I had in my head of what the La Marzocco factory some ten years ago, at Ninth Street Espresso in New York, as I looked upon the “Handmade In Florence” emblem on our GB5.
The sunlight shines bright through large open windows in the enormous factory, beaming on people that take their craft seriously, and who clearly enjoy being there.
Zachary Carlsen is a co-founder and editor at Sprudge.com. Read more Zachary Carlsen on Sprudge.
The post Handmade In Florence: Meet La Marzocco Technicians That Build Espresso Machines appeared first on Sprudge.